Background
Aluar Aluminio Argentino S.A.I.C. (Aluar) is the only primary aluminium producer in Argentina. In addition to a large business in ingot and extrusion billet, the smelter also supplies Aluar’s rolling operations at Abasto. Aluar’s rolling facilities include a hot reversing mill, a cold mill and three foil mills.
Because our Process Engineering team has experience of world-class rolling operations, the team at Aluar contacted us to help them with rolling process improvement. The aim was to improve quality and productivity with a view to increasing their market share.
How we were involved
During the first visit to Abasto, at the start of the rolling process improvement project, Dan Miller and Kyle Smith audited the rolling operations. They made assessments of the standards achieved against operations with similar equipment and against world class standards. They also analysed the material flow and material storage.
From these asessments, Dan and Kyle identified opportunities for improvement, and they worked closely with the team at Aluar to prioritise and to implement their ideas to improve productivity, yield and product quality.
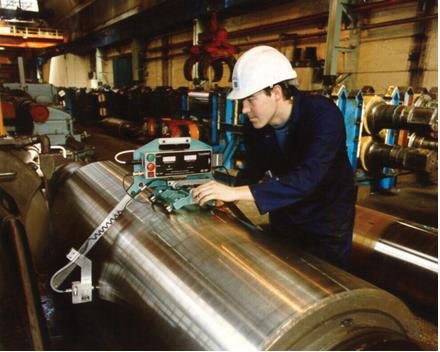
Outcome
A rigorous approach to defect classification was established in order to accurately identify the reasons for scrap generation and so begin to improve recovery. Statistical Process Control, with highly visible performance measures, was introduced and the teams were taught effective problem solving techniques.
Further improvement ideas were generated around the design and maintenance of the hot mill and its cooling system, part of which included a cooling analysis using Innoval’s spray modelling capabilities. Aluar personnel have continued to develop the process and implement improvements.
We’ve been delighted to continue working with Aluar by providing several strategic studies. These have included a study on the benefits of alloy optimisation from our Materials Development team, led by Dr. Gary Mahon, as well as looking at the strategic investments necessary to expand the hot rolling capacity in the longer term.
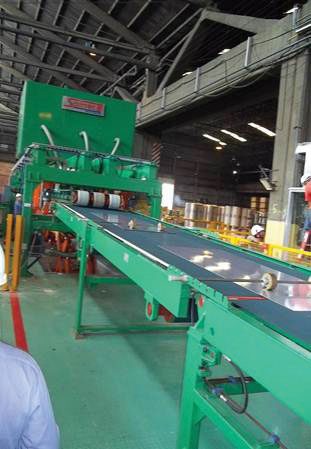
Services Involved
- Process Improvement
- Process Models
- Rolling
- Materials Development
- Investment/Upgrade support
This case study appears as an article in the 2013/14 edition of ‘innform’; the newsletter of Innoval Technology.
It is a pleasure to interact with people like Dan, Kyle and Gary. They are very professional in their approach yet open and friendly, so it’s easy to build a rapport with them. We value the interactions we have with different Innoval consultants as they help us to identify new issues and plan for the future. We value their comprehensive range of skills and extensive industry experience, and can rely on them to give us sound independent advice.
Member of the Aluar team