Background
A large part of our work is collaborative research to help our clients develop new products. Whilst this is always carried out under a Non-Disclosure Agreement, sometimes we’re able to report our findings at industry events.
In June 2018 we presented a joint paper with AMAG rolling GmbH (AMAG) at the 10th Aluminium Brazing Congress in Düsseldorf. This paper summarised research into the creation of a higher strength vacuum brazed AA3xxx series alloy with a sacrificial ‘brown band’.
How we were involved
Historically, the aerospace industry uses the vacuum brazing (VB) process and clad AA6xxx series alloys for their aluminium heat exchangers. This gives a high strength T6 product. However, it requires additional surface protection to achieve the required level of corrosion protection.
AA3xxx alloys are usually processed using controlled atmosphere brazing (CAB). Consequently, a high strength VB AA3xxx series alloy with good corrosion resistance could lead to new opportunities in aerospace applications.
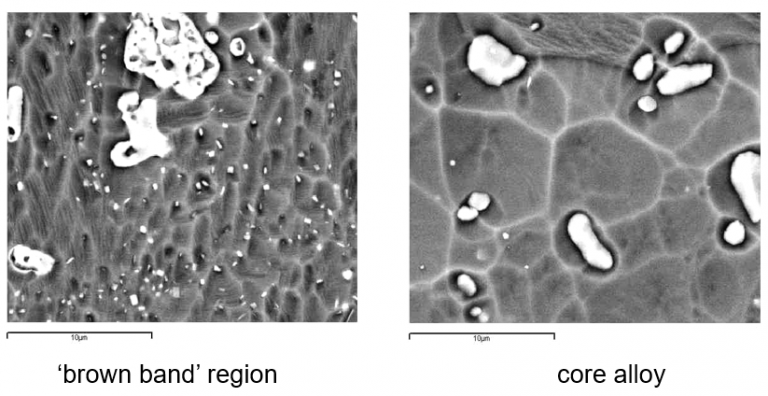
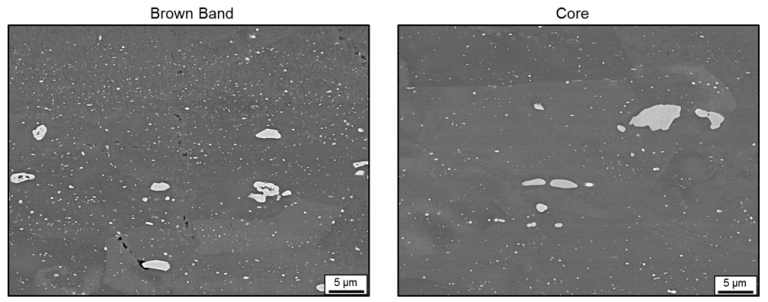
The research centred around increasing strength with a two-stage homogenisation while retaining the sacrificial ‘brown band’ region. This is a feature of many controlled atmosphere brazing (CAB) alloys.
The brown band forms during brazing. It consists of densely precipitated particles containing aluminium, manganese and silicon (AlMnSi). This band is typically a few tens of microns thick at the surface of the core, adjacent to the cladding layer. It impedes corrosion by containing it within the brown band region, rather than allowing it to penetrate the bulk structure along the grain boundaries.
For this project, AMAG modified the composition of an AA3xxx alloy to increase the strength. They then supplied us with rolled material. Using our lab-based aluminium brazing furnace to produce both VB and CAB samples, we analysed the diffusion profiles for silicon, manganese and magnesium. We also characterised the microstructure of the brown band in both sets of samples by scanning electron microscopy.
Outcome
Amongst other things, the trials showed that the VB AA3xxx material was stronger than CAB material. Furthermore, the brown band in the VB material was consistent with that found in the CAB material in terms of thickness and microstructure. However, homogenisation decreased the effectiveness of the brown band.
Following the positive results from this collaborative research, future work could determine the effect on strength and corrosion resistance of adjusting the copper levels in the core alloy.
Services Involved
- Materials Testing
- Materials Development
This case study appears as an article in the 2019 edition of ‘innform’; the newsletter of Innoval Technology.
In Innoval we found a valuable sparring partner in addition to AMAG´s R&D team. The longtime expertise of Innoval is beneficial for our strategic projects.
Gerhard Hanko, Head of Technology Heat Exchanger Materials, AMAG rolling GmbH