Posted on: 28th June 2016 by Dr. Junjie Wang
As a technical consultancy it’s really important that we keep up to date with the latest developments in light metals. One of the ways we do this is by leading and participating in pre-competitive R&D projects.
Most of the projects we have been involved with over the last 10 years have had either an automotive focus, or have been to do with the exploitation of the unique properties of anodised aluminium films.
This blog post describes some of the work we did as part of the INCAS (Integration of Nanoreactor and multisite CAtalysis for a Sustainable chemical production) project. The INCAS project involved the exploration and development of anodised aluminium substrates as a potential catalyst support in downstream industrial applications.
Free-standing membranes
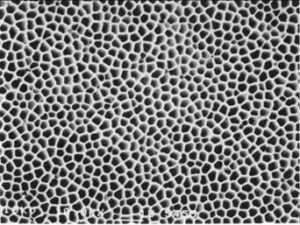
Initially the project focussed on the development of a free-standing anodised aluminium membrane film. This is a 60µm thick alumina-based material produced by electrolytic processing. It has a high density of flow-through channels (Figure 1).
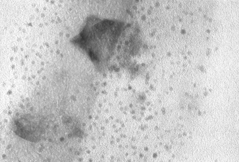
While we successfully produced these materials, our project partners deposited or coupled Palladium-based nano-particle catalysts within the pores of the membrane (Figure 2). They then tested their catalytic performance characteristics.
In a number of cases the anodised aluminium substrate had distinct performance advantages. However, in some instances, chemical and mechanical instability issues relating to the membrane material had to be addressed. Consequently there were a number of anodic material modifications, system reconfigurations and alternative developments.
In the case of material modifications, thermal processing significantly enhanced the chemical stability of the anodic membrane material. This resulted in the formation of more chemically resistant phases. Furthermore, system reconfigurations enhanced the mechanical stability by producing tubular anodic membranes (Figure 3a) and incorporating them within protective steel mesh tubes (Figure 3b).
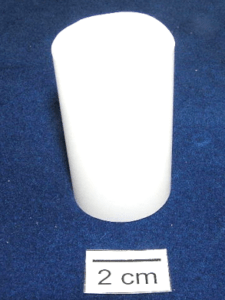
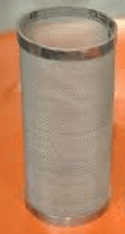
However, despite these approaches, underlying concerns over the free-standing membrane stability continued to exist. This led to two completely alternative developments from that originally envisaged.
These were the anodising of aluminium foam material (Figure 4), and the polymer templating of an anodic film structure to produce a sheet-like polymer substrate with a high surface area.
Anodised aluminium foams
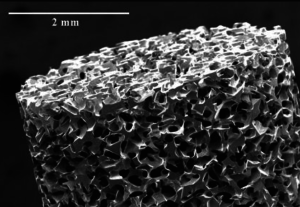
A European Roadmap study on heterogeneous catalysis for process intensification identified the approach of using metal foams.
Consequently, we developed suitable anodic film structures on mechanically stable aluminium foam. The project partners successfully impregnated the anodic films with catalyst nano-particles and assessed their performance. They found that, from a technical point of view, such a solution to mechanical and chemical stability concerns had clear merits.
Unfortunately, wider economic considerations by downstream partners resulted in the postponement of future development work in, for example, industrial catalysis. However, several niche applications are being considered which were beyond the scope and time frame of the project.
Polymer replication
Polymer replication involves ‘flooding’ the pores of the anodic membrane with a polymer. As a result, the topography of the membrane is perfectly replicated in the polymer.
Our project partners considered this to be a completely novel and alternative approach. They found the idea of continuously producing large scale coils of replicated polymer films with controlled microstructures for catalyst deposition (or incorporation) especially promising.
In addition, this polymer replication approach from anodised substrates, has the added potential of being mechanically flexible. As such, it could be reconfigured in several ways e.g. spiral wound modules which could be retrofitted into existing plant systems. Although promising in principle, this latter approach requires more extensive development and this was beyond the scope of the project.
Project conclusions
The project determined that the use of the free-standing anodic film membranes as originally envisaged was not considered fit for the specific project application. However, with the developments undertaken and alternatives explored by Innoval, niche applications and alternative approaches employing anodising technology clearly had technical merit and longer-term development potential.
Also, it should be noted that the scientific and technical literature for much broader and functional applications of anodised anodic films continues to be highly active, and has been for over a decade.
Finally, I would like to express thanks to the EU for project funding and to my European project partners for their collaboration: CSIC-ITQ (Spain); Sasol (UK); TU/e (Netherlands); Hybrid Catalysis (Netherlands); TUM (Germany); Bayer Technical Services (Germany); Shell (Netherlands); INSTM (Italy); Repsol (Spain); and ERIC (Italy).
Conventional anodising
As well as specialised development work such as this, we can support conventional anodising operations. For example, we can carry out process audits and training courses. Please get in touch if you’d like to know more.
This blog post was originally written by Dr Eoghan McAlpine who has now left the company. Please contact Dr Junjie Wang if you have any questions.