Work with us to access our world-class aluminium knowledge, combined with expertise in polymers, surface treatment and joining technologies.
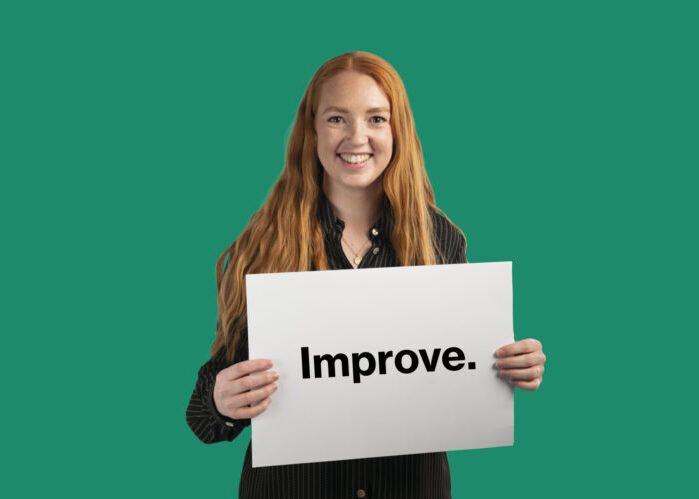
Improve your quality for a consistently good product.
We have extensive knowledge of microstructural development during processing and its effect on product performance. We also understand surface modification during finishing operations. By working with us you will gain an in-depth understanding of where in your process these are controlled so you can ensure a consistent, quality product.
Did you know our in-house laboratories can analyse your material to solve a problem or answer a question? We will turn your samples around quickly and give you advice as well as test results.
Develop new products faster.
Supplementing your technology team with our aluminium expertise could shorten your development time and increase your speed to market. We’ve had years of experience leading development programmes, and we’re currently responsible for managing several high-profile, government-funded projects.
Our materials knowledge is the key to our business, so we make sure we know and understand the latest industry developments. Furthermore, we have many long-term collaborations with universities and research centres. This means we’ll always give you the most up-to-date solutions.
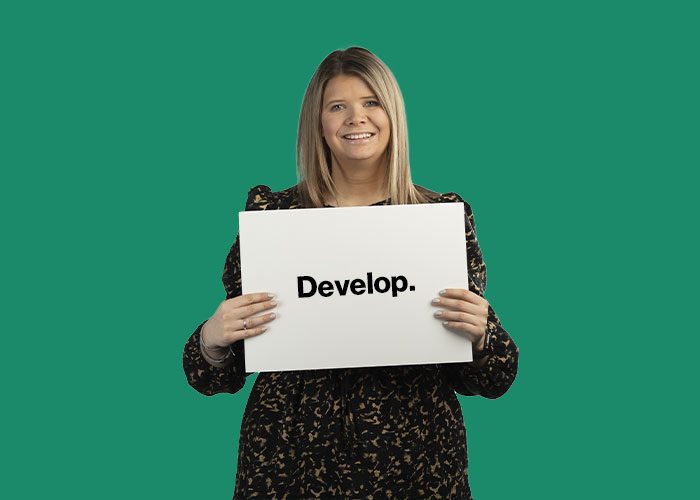
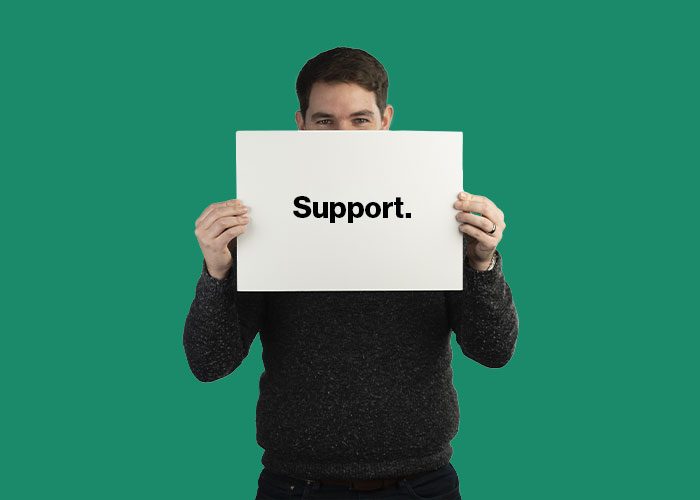
Give your customers unrivalled support and become their preferred supplier.
You could add value to the service you give your customers by offering our unparalleled knowledge and experience as part of your after-sales service. Our experienced team is used to solving process and product performance problems in a wide range of industries, and we’ve been doing it for many years.
Invest in new technologies to stay ahead.
In order to stay ahead of the competition you need to know which technologies are ‘state-of-the-art’. Because of our experience and industry-wide perspective, we can help you identify which new developments to invest in and how this investment will affect your bottom line. Detailed cost modelling, using our own innovative software, allows us to do this. In effect, it reduces the risk.
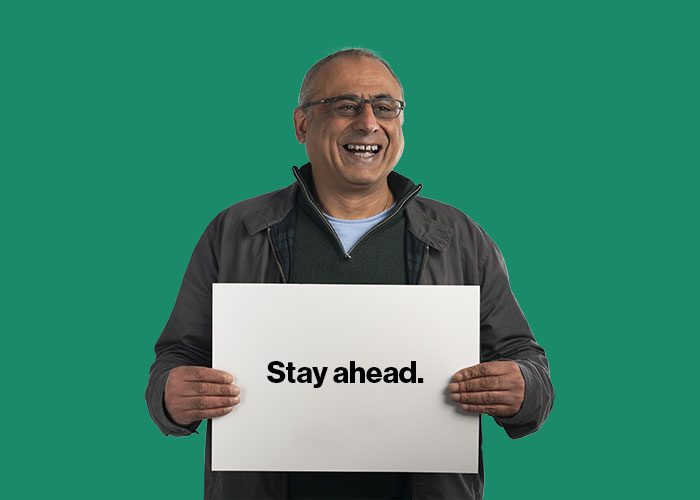