Posted on: 31st March 2017 by Rachel Wiffen
As a technical consultancy we don’t manufacture products. Instead our products are the reports we send to clients on completion of a project. You might think ISO 9001 certification is not quite as critical for us as it is to a company making physical products. However, as I will explain here, it’s just as important.
Establishing a Quality Management System
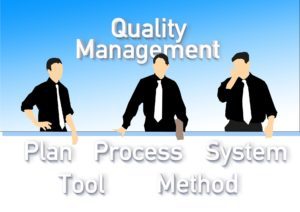
Very shortly after the creation of Innoval in 2003 we decided to establish a Quality Management System (QMS). We designed the scheme to reflect the way we already worked. However, we also made it compliant with the requirements of ISO 9001 certification. We call our system the IBMs, or Innoval Business Management system.
Back in 2003 everyone at Innoval used to work at Alcan’s excellent research centre in Banbury. Therefore, we were already familiar with the ‘formal report writing followed by review and approval’ way of working. Making the transition to a formalized ISO 9001 system really wasn’t such a big step.
The single greatest aid in the whole process was the creation and ongoing development of an electronic database system. We’re able to access this via our company Intranet. Our in-house expertise for software creation has been a really crucial feature in our development. Now we have a massive library of records for everything we have done for all our clients.
Auditing
Since the start, LRQA has audited us. We find the approximate 9-monthly audit cycle (certificate renewal every 3 years) an appropriate frequency. Furthermore, we feel that their external view and opinions are both well-balanced and useful.
How we use ISO 9001 certification
We use ISO 9001 certification to control the processes we use to make our products. In our case, that’s our reports. I suppose that is where the biggest misconception about quality management systems arises. A QMS is not specifically about putting a ‘badge’ on a product. In fact, this is not permitted. 9001 is about the system that produces the product; how is it managed and controlled? How is it reviewed and improved?
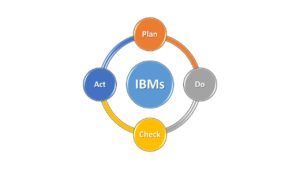
At Innoval we apply the oft-mentioned ‘Plan-Do-Check-Act’ time and time again to help make the system (the way we do things) more robust.
Every product we create, which in our case is a report of some type and format, goes through the same ‘life cycle’ process. This culminates with a final review and approval, by someone other than the author, before we send it to the client.
How does ISO 9001 certification benefit our clients?
Quite simply, ISO 9001 certification means that at least one other pair of eyes, in addition to the qualified and highly-skilled person doing the writing (and most probably, performing the associated work) will critically review every report issued by Innoval. This ensures a degree of normalisation with the content and style, for example, by using our corporate documentation. It also means that the client’s report benefits from the broader knowledge and experience within Innoval.
What’s next?
ISO 9001:2015 is now the standard. We are currently certified to the 2008 version of the standard. The new version, in common with a great number of ISO standards, incorporates an element of risk assessment to drive the continual improvement of the system. Companies must be able to identify risks to the business and put control measures in place.
There is a grace period of 3 years to convert to the new ISO 9001 certification standard. Exactly how we achieve this is a work in progress at the moment. Thankfully, our good friends at LRQA continue to provide us with useful guidance and support. A later blog post will let you know how we’ve fared!
Is ISO 9001 certification worth the effort?
To our clients? Without a doubt. Every product is of a high standard and fully traceable. Furthermore, we have a record of everything we do (and have done) for every client. This is available for future reference if required.
For Innoval? Yes again. The rigour of a periodic external audit causes us to keep our systems up-to-date and maintain the levels of performance that might otherwise gradually become comfortable and degrade over time. The challenge to continually improve and to be able to demonstrate this works for us.
If you want to know more about what we do, or you’d like further information about how we set up our Quality Management System, please send us an email.
(Figure1. from www.pixabay.com)
This blog post was originally written by Andy Darby who has now left the company. Please contact Rachel Wiffen if you have any questions.