Posted on: 16th January 2017 by Kyle Smith
On the first day of our Aluminium Rolling Technology Course I run a session entitled “Machinery and Process Overview”. Part of this covers the history of metal rolling from the first known drawings of a mill to the state-of-the-art rolling equipment available today. Metal rolling has an interesting history and I will share some of it in this week’s blog.
An easier way to form metal
Early metal workers found that forging a shape with hammers from a simpler cast shape created objects far stronger than those formed by casting alone. However, hand hammering was laborious even for soft metals, so pressure grew to create machines to assist with the forming process.
Early equipment for metal rolling
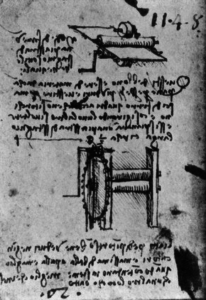
The equipment that followed to create sheet products proved to be of very simple design.
It is not known who created the first rolling mill. However, one of the earliest drawings is by Leonardo da Vinci. It even shows the need for larger diameter backup rolls to support longer, smaller diameter work rolls, Figure 1.
15th – 17th century
In the middle of the fifteenth century small mills produced gold lace, and other decorative work, in soft metals.
However, as these techniques became more widely known, demands for products coming from metal rolling increased. There is evidence for rolling of lead and tin on simple 2-high mills with cast-iron rolls at the beginning of the seventeenth century.
At this point rolling mills did not process the high volumes of metal that we see today. In addition, the required quality of these early products was ‘poor’ if we measure it by today’s exacting standards. However, no-one had developed the applications that needed higher quality material. Energy was also a big consideration if this technology was to be expanded further.
By the end of the seventeenth century, it was possible to cast larger iron rolls and therefore build heavier mills. Horses and then water wheels drove these mills.
18th – 20th century
During the eighteenth century, 4-high designs appeared (300 years after da Vinci). This was because people discovered that smaller diameter rolls required less load to reduce the metal thickness. Consequently, it was possible to use a lighter frame.
At the end of the eighteenth century, with the availability of steam power, the mills started to resemble their modern counterparts. During the nineteenth century and into the twentieth century, the size and power of mills increased with little change to the main design. Steam engines were capable of delivering in excess of 10,000 hp. One example of this is the 12,000 hp (8.9 MW) River Don Engine built by Davy Brothers in 1905 to roll armour plate. However, more efficient electric motor technology slowly replaced steam power in the twentieth century.
Interestingly, we have our own connection with eighteenth century metal rolling here at Innoval. Our former Managing Director, Dr Tom Farley’s great grandfather, Reuben Farley, started a company in 1861 which manufactured rolling mills and rolls in West Bromwich, UK. The company was “Taylor and Farley”.
Tom Farley is our expert in rolling mill vibration. I’m sure Reuben Farley would be very proud to know that metal rolling expertise still exists within the Farley family.
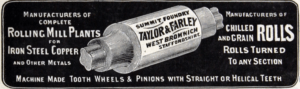
Today’s rolling mills
The basis of design for today’s equipment is not too dissimilar to early designs, particularly when you consider a basic 2-high mill. It just uses different types of materials and designs of roll stacks. However, today’s mills are now designed for processing a multitude of metals for extensive end-user applications. In some cases there are more than 20 rolls in the roll stack. This clearly demonstrates that mill designs and their requirements have moved on substantially from the early basic designs.
Today we produce much higher quality products which have exacting standards in dimensional accuracy, surface and material properties. All of these need to be considered in the design of new mills, be it for plate or coil products.
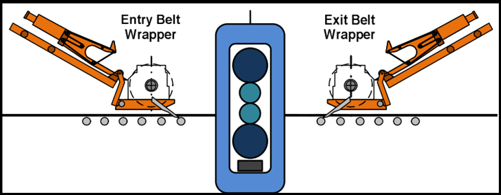
The mill in Figure 3 has the capability to produce high quality thick and thin plate and sheet (coil) products. The belt wrappers in this case are located on both entry and exit sides of the mill. These belt wrappers are designed to move in and out as and when required to produce either plate or coil products. With capacities in excess of 200 Kt per annum, this design represents a major leap in technology from where it all started back in the time of Leonardo Da Vinci.
Aluminium Rolling Technology Course
Our Aluminium Rolling Technology Course covers all the key aspects of hot and cold rolling of aluminium flat products. My colleagues and I write and deliver the modules. Between us we have a huge amount of industry experience. We’re very familiar with the day-to-day issues of a rolling plant, and we’ve created this course to help you solve them. Many of the presentations are supplemented with hands-on workshop sessions.
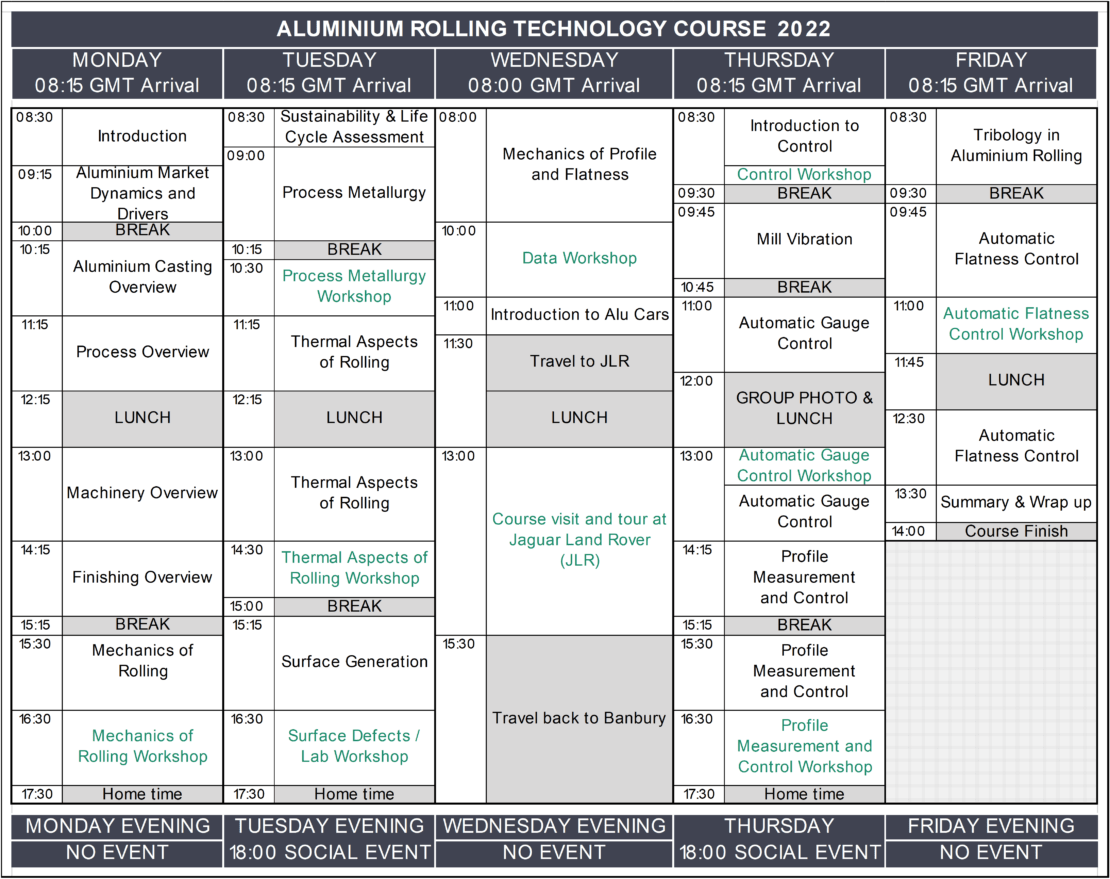
The course takes place twice a year here in Banbury or online. You can download a registration form (which contains the timetable and information about the cost) here. Finally, you might be interested to know that the course is recognised by the Institute of Materials, Minerals & Mining (IOM3) as Professional Development.
This blog post was originally written by Mark Rewaj who has now left the company. Please contact Kyle Smith if you have any questions.