Posted on: 30th January 2017 by Sunil Khosla
Molten metal cleanliness is one of the key challenges for most casthouses. They must produce a slab with a sufficiently low level of hydrogen, alkali metals (mainly sodium) and inclusions to make the finished product suitable for its final end use. This is particularly important where the slab will be rolled into sheet for the manufacture of beverage cans or foil.
Molten metal cleanliness needs to be correctly managed, through a combination of having the right equipment and ensuring that it is correctly operated.
Initial molten metal cleanliness
It is important to start by ensuring that the melting and holding practices employed prior to casting are as close to best practice as possible. The higher the molten metal cleanliness is prior to the degassing/filtration operation, the cleaner it is likely to be after treatment. Some key areas that typically require careful management are:
- The purchase of primary metal, hardener materials and scrap from proven/qualified sources
- The addition of alloying elements at the correct temperature (particularly magnesium)
- Thorough skimming and regular cleaning of the furnace
- Employing the settling practices as appropriate
- Minimising metal turbulence, particularly in the transfer launders.
Degassing
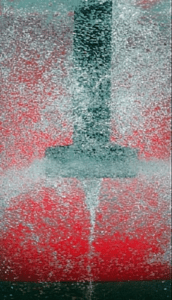
Depending upon the product, the next critical operation is likely to be that of the degasser. There are many different types of degasser, but most rely upon a sub-surface spinning rotor.
The rotor injects a chemically active reactant (normally either chlorine gas or a solid salt flux) mixed with a carrier gas (such as argon or nitrogen) as fine bubbles into the molten metal. The key to operating such devices for optimum efficiency is to use a rotor design and practices that generate a small bubble size with a long bubble sub-surface residence time.
A well operated degasser should be capable of reducing the incoming hydrogen concentration by at least 50%. In addition, it should also reduce the alkali metal and inclusion levels. However, whilst a degasser will remove some inclusions, filtration achieves most inclusion removal.
Filtration
For inclusion critical products, some casthouses use a deep bed filter. This normally involves filtering molten aluminium through a bed of varying size ceramic media. Whilst these are normally very efficient (typically 85% plus), they can be expensive to operate. This is due to the floor space required and the limited life of the filtration media. They typically require regular replacement and disposal.
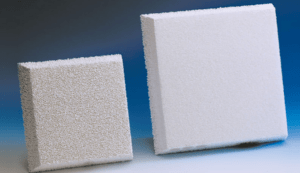
The final filtration step is generally a ceramic foam filter (CFF). This is a single use disposable filter made of a tough porous ceramic foam with tightly controlled pore sizes. These are often the sole filtration equipment in many casthouses due to their simple operation and good results for short runs. Three critical parameters for a CFF are:
- The filter area – the larger the area, the larger the potential metal flow rate. However, large tiles can be difficult to handle due to the risk of damage.
- The pore size – the smaller the pore size the more efficient the filter. However, it’s more likely to block mid cast.
- The thickness – the thicker the filter, the better the filtration efficiency. However, it could be more difficult to initially prime it.
For some extremely critical applications, it’s common to use more expensive ceramic tube filters.
Disturbances during filtration
Whichever filters are used, care needs to be taken to ensure that the filters aren’t subject to excessive vibration or metal level changes. These “disturbances” can cause a release of inclusions which may end up in the finished product. Good process control downstream of the final filtration device is particularly important. This should include careful launder preparation with special attention if any repairs are required. Additionally, casthouse operators should be careful to minimse turbulence in certain areas, such as around the metal distribution bags.
An input of very dirty metal will overwhelm even the best available filtration technology. Therefore, the importance of correctly conditioning the metal prior to filtration cannot be overstated. The cleaner the metal entering the filter, the finer the filters that can then be used, resulting in “even cleaner” metal exiting the filter.
Casthouse expertise
To summarise, there is no “silver bullet” to achieving good molten metal cleanliness. However, using the correct equipment in conjunction with a knowledgeable workforce who are capable of maintaining good process control is the best way to ensure success.
If you need further information or support to achieve good molten metal cleanliness, please do not hesitate to contact one of our Casthouse Experts. We can assist you to optimise your process to meet your metal quality requirements.
(Circular image shows an aluminium ingot cast by Novelis at Latchford. The image is from www.thinkcans.net)