We’ve been investing!
Find out about our new equipment.
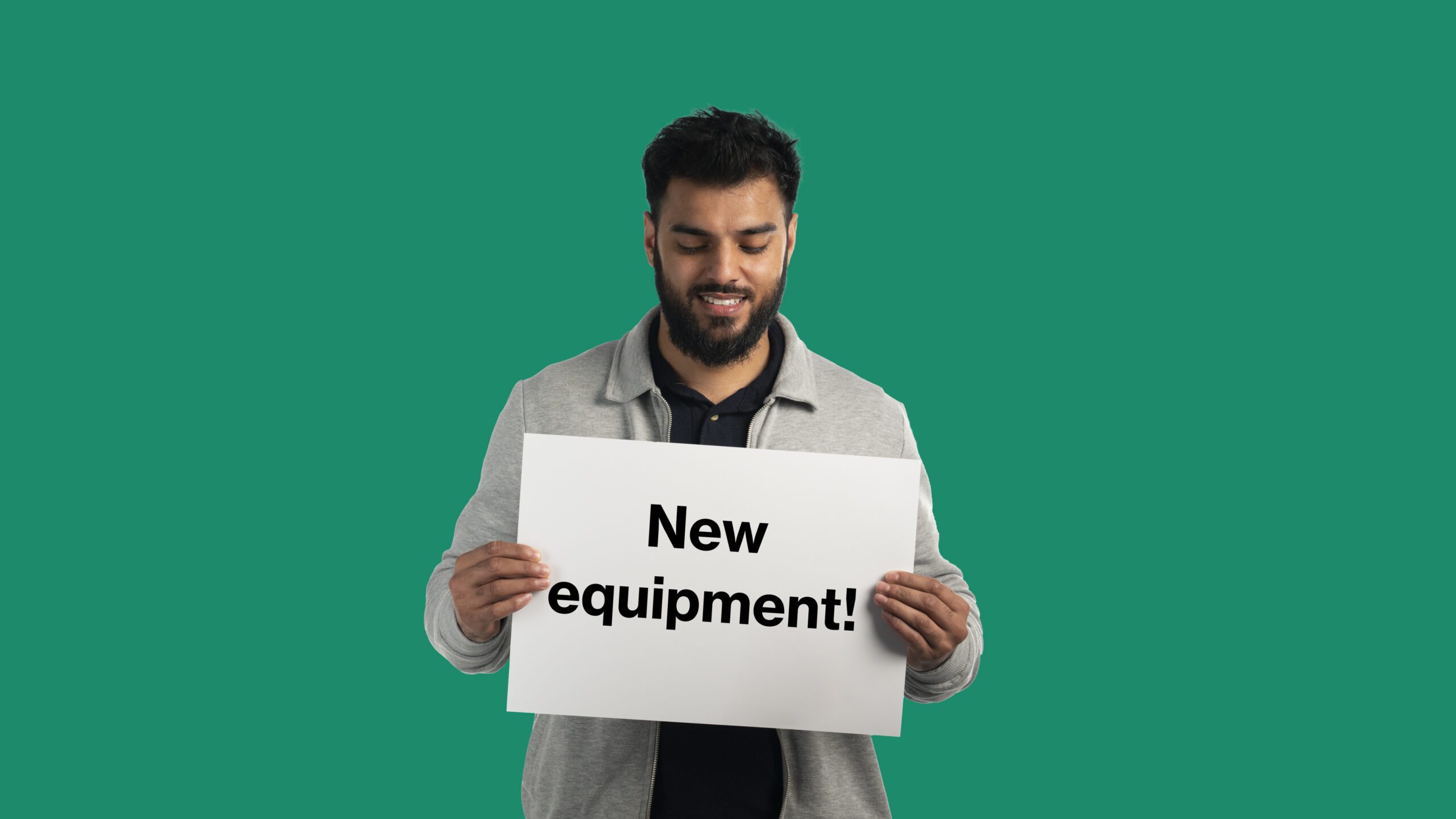
We’ve been providing advanced materials testing and
characterisation solutions for the global aluminium industry for the past 20 years.
We are now investing in new equipment so that we can continue to provide the latest and most complete range of services.
This is what we’ve added to our portfolio:
Tensile Tester | Enamel Rater | Surface Profilometer | Spectrophotometer | JMatPro®
Here’s a list of the analytical techniques we offer.
General testing.
Optical microscopy.
Optical Microscopy is normally the first stage of materials characterisation. It can give the general microstructure of a sample at up to 1500x magnification. Not only does it give the microstructure, but it also has the ability to analyse both the grain structure and particle distribution of a sample. In addition to all of this we can use optical microscopy to take thickness and area measurements of cross sectioned samples.
Scanning electron microscopy (SEM).
SEMis a very powerful technique in which an electron beam can be used to study the surface topography of a sample. The sample then interacts with an electron beam to create a high-resolution image of the sample with a very high depth of field. X-rays are also produced during the interaction of the electron beam with the sample. They give us qualitative information about the sample composition (EDX). We can look at the composition of hundreds of features at once using our ‘SEM feature’ analysis or use ultra-low kV SEM to look at surface defects.
Transmission electron microscopy (TEM).
TEM is an even higher resolution technique where a beam of electrons shines through a very thin sample allowing us to see down to the atomic level. This is very helpful to look at the precipitates in some alloys that provide strength, or to look at very thin surface structures that can’t be resolved any other way.
Mechanical testing.
This covers a wide range of testing that can be used to assess the mechanical properties of a material e.g. tensile strength or the hardness of a material. Examples of tests we can perform include: Hardness, Tensile Testing, Kahn Tear Testing, Thin Gauge Testing, Elevated Temperature Testing and Earing and Erichsen cupping.
Surface analysis.
We offer a wide range of surface analysis to help you understand and control the surface quality of your products. This includes surface morphology, surface roughness, surface chemistry, surface/near-surface microstructure, surface wettability, residual surface carbon, lubricant coat weight, oxide/anodic film thickness, surface cleanliness, quality of surface chemical pretreatment (coat weight, thickness and distribution), paint adhesion, level of coating curing and quality of adhesive bonding, etc.
We use powerful techniques to get the most out of surface analysis, including high-resolution low accelerating voltage SEM (low kV SEM), analytical TEM, sample cross-sectioning using ultramicrotomy and Focused Ion Beam (FIB) milling, Fast Fourier Transformed Infrared spectroscopy (FTIR), White Light Interferometry, Goniometry, Spectrophotometry, Colourimetry, Thermo-mechanical Analysis (TMA), Glow Discharged Optical Emission Spectroscopy (GDOES), X-ray photoelectron spectroscopy (XPS) and X-ray Fluorescence (XRF), etc.
Corrosion testing.
This is used to determine whether the material or component will be susceptible to the environment in which it is to be used or compatible with other materials in the system. It can be used to determine the mode of attack, (pitting, intergranular, trans-granular and exfoliation, etc.) and its severity using a wide range of techniques including electrochemistry, immersion or salt spray testing.
Thermal analysis.
At Innoval, we use both differential scanning calorimetry (DSC) and thermo-gravimetric analysis (TGA) to look for changes in structure. DSC measures the smallest changes in temperature to allow us to detect/measure phase changes and the onset of melting/solidification. TGA measures subtle differences in mass to give information on phenomena such as adsorbtion/desorbtion and thermal decomposition.
Composition.
Inductively coupled plasma optical emission spectroscopy (ICP-OES or ICP-AES) is a major technique for elemental analysis. The sample is normally first dissolved and then mixed with water before being fed into a plasma source, where the atoms in the plasma emit light with characteristic wavelengths for each element. This light is recorded by one or more optical spectrometers and, when calibrated against standards, the technique provides a reliable quantitative analysis of the original sample.
Product specific testing.
Packaging.
To support the packaging industry (beverage, food and healthcare) we are able to provide a range of tests specific to cans and foil. These can be to qualify a new material, supplier or process route. We also carry out examination of defects and failure analysis.
Coated/anodised products.
We have a range of tests available to international standards to determine whether a coating is suitable for the application. These include determination of the type of coating, thickness measurements, whether the material is fully cured, adhesion, hardness, formability and impact resistance of a coating. For anodised sections we can also look at the size and distribution of asperities within the anodic film.
Heat exchangers.
Understanding your product at the microscopic level can lead to big improvements. For example, the shape and distribution of silicon particles in the cladding can affect its fluidity once molten, and the thickness of the oxide film can affect brazeability (wettability). We have both the facilities and the expertise to investigate these two features, and many more. As well as providing you with analysis results, we’ll advise on what you can do to improve your product.
Alloy development & pilot processing.
Through our strategic partner network, we have access to laboratory scale casting, rolling and extrusion facilities to support alloy and materials development projects.