Posted on: 16th December 2016 by Kyle Smith
Innoval has developed a number of models to help solve production problems quickly and effectively. One of these models is the winding model which we use to predict the contact pressures between laps of a sheet of aluminium wound onto a core.
Our Engineers use our models when solving problems for our clients. However, they’re available to buy too.
Winding problems
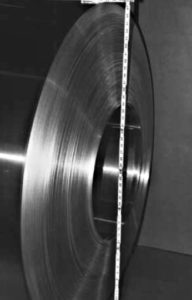
Winding happens in processes such as rolling mills, slitters, levellers and rewinders. It’s a relatively simple process but, if done badly, can result in a lot of high-value scrap. A badly wound coil, for example, can collapse the core because there’s too much winding tension.
At the other extreme, a coil’s laps can slip sideways off the core to cause telescoping. This happens when there’s not enough winding tension to create sufficiently high contact pressures.
You can control telescoping, lap slipping and buckling by continually varying the tension during winding to produce a coil that is stable and of consistent winding quality.
Two types of winding model
We’ve created two types of winding model; a Finite Element Analysis (FEA) and an analytical model. Figure 2 shows an FEA simulation where a strip is wound onto a core.
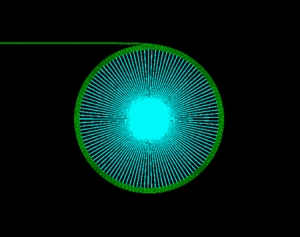
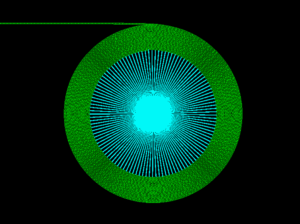
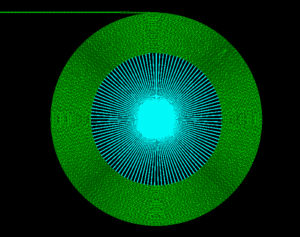
Figure 2. An FEA simulation of winding at the start, middle and end of the winding simulation.
In Figure 3 the contact pressures derived from the analytical model vary radially from one lap to the next.
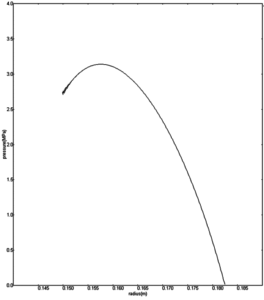
Both models give almost exactly the same predictions. However, we developed the analytical model because it is much faster computationally. Furthermore, we’re also able to sell it as a stand-alone product rather than clients having to invest in an FEA package to run the FEA winding simulation.
Multi-slitting
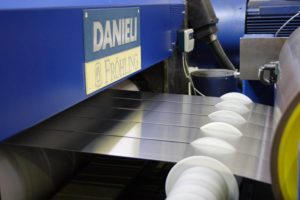
We’ve extended the analytical model to incorporate centrifugal effects, air entrainment, flatness and thickness profiles of strip. We use it mainly to design winding tension strategies for multi-slitting.
Multi-slitting transforms a wide sheet of aluminium into a series of narrow strips. The slit material is wound onto individual cores to form a “ring”.
A single arbour holds all the rings which ensures they rotate at the same rate. However, problems occur when there’s a thickness variation across the sheet resulting from the strip profile. An ironing roll compresses the larger diameters of the thicker strips to smaller diameters. However, there’s a limit to how much compression can take place to account for the incoming strip profile.
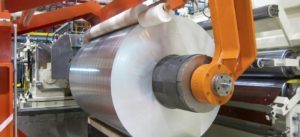
With the use of the winding model, you can design the tensions during winding to maximise the range of profiles or the “process window”. When the incoming strip profile falls outside this window, then loosely wound rings will collapse. As a result, if this occurs during slitting, some of the rings may be scrapped or, in extreme cases, the whole coil.
As this example illustrates, computer modelling can help achieve significant savings in process costs. Finally, if you would like to know more about the winding model, or how our engineers can help solve your production problems, please contact us.
This blog post was originally written by Dr Rade Ognjanovic who has now left the company. Please contact Kyle Smith if you have any questions.