Posted on: 8th March 2019 by Dr. Junjie Wang
In a previous blog about aluminium pretreatment, I looked at how we prepare aluminium for painting, lacquering or adhesive bonding.
If we want to produce an aluminium product that lasts longer than it takes for a car to roll out of a showroom or a building façade to be enjoyed for more than a few months (fig.1), then we must ensure that we get the aluminium foundations right. This means making sure that when we come to apply that wonderful bright green paint or that super strong glue, the aluminium surface is just right.
The ‘just right’ aluminium surface
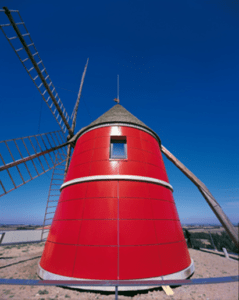
Previously I have discussed the various processes we need to get this “just right” surface:
Cleaning – to remove debris or residual oil left on the surface after the aluminium has been processed.
Etching – eliminating fragments of loose, malformed oxide that can encourage corrosion.
Pretreatment – stabilising the aluminium surface to provide a consistent layer that will interact in a positive way with paints, lacquers or adhesives.
The image below (fig. 2) is a transmission electron micrograph showing a cross section of what a “just right” surface looks like.
It shows a largely featureless metal with a 10 nm thick pretreatment layer. The pretreatment looks uniform and it follows the metal surface nicely. Don’t worry about the dark bands, they’re caused by the viewing technique.
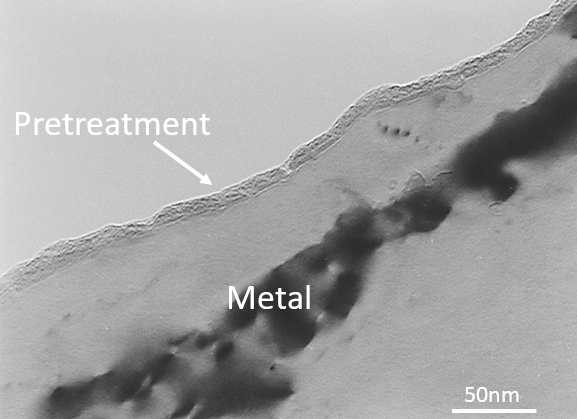
Why pretreatment is so important
So why do we go to all this trouble? It seems almost unbelievable to think that a layer 10,000 times thinner than a human hair could be so important for holding a car together or stopping windows in a skyscraper from falling out, but it’s true.
What we’re doing when we apply paint or adhesive to an aluminium surface is kicking off chemistry between the two materials. The aluminium producer must ensure that their material has the right chemical groups on the surface. The adhesive/paint/lacquer supplier must see to it that they have components that can bond with the surface chemical groups.
From the adhesive and paint side we hear terms such as epoxy, ester, urethane and isocyanate. These are all chemicals that, under the right circumstances, start reacting both with themselves and with chemical groups on the aluminium surface (fig. 3).
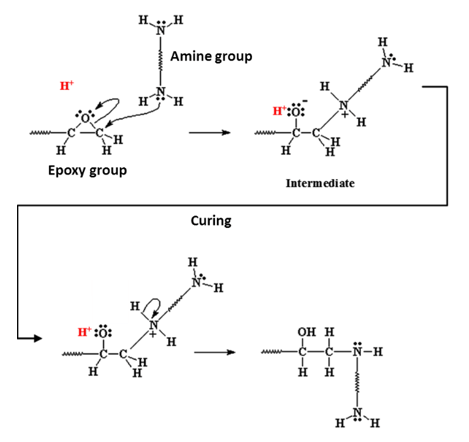
When they react with themselves it’s called curing. This gives mechanical strength to the adhesive layer or paint film. Of course, just having a strong adhesive doesn’t mean you can form a strong bond between, for example, two parts of a car’s body. This is where the reaction with the chemical groups on the metal surface comes in. When the epoxy etc groups of the adhesive react with hydroxyl (oxygen bonded to hydrogen) groups on the surface we form a very strong and chemically stable linkage between metal and adhesive. These hydroxyl groups are present on the metal surface because of cleaning and pretreatment.
Optimum number of hydroxyl groups
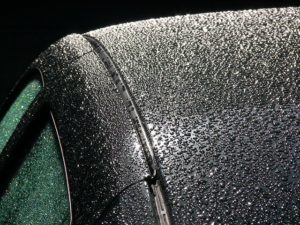
Getting a good bond between metal and adhesive is not simply a question of having the highest number of hydroxyl groups on the aluminium surface. There is an optimum concentration.
If the hydroxyl groups on the surface exceed the optimum number, then the surface will, over time, soak up water and disrupt adhesive bonds. This can cause joint failure. People seem to think that if we paint a surface or make an adhesive joint we are keeping water out. If only it was that simple. In fact, all paints and adhesives allow water to pass through to the metal surface. However, that’s a point for discussion in another blog.
Do you want to know more about getting paints and adhesives to work properly on aluminium? If so, you might want to attend this training course. To find out more, complete the form in the link or use our Contact page. Alternatively, if you have a process or a product issue relating to surface treatment, have a look at this page. It describes the many other ways in which we can support you.
This blog post was originally written by Dr Colin Butler who has now left the company. Please contact Dr Junjie Wang if you have any questions.