Posted on: 24th November 2016 by Kyle Smith
This blog will cover some of the computer based methods we use to get the most out of aluminium rolling and finishing processes. Using computer models, such as Finite Element Analysis (FEA) models, increases understanding and reduces the number of online trials. As a result, they reduce the cost of process optimisation. It’s true to say that FEA models are a significant part of our ‘tool box’.
FEA models to predict alligatoring
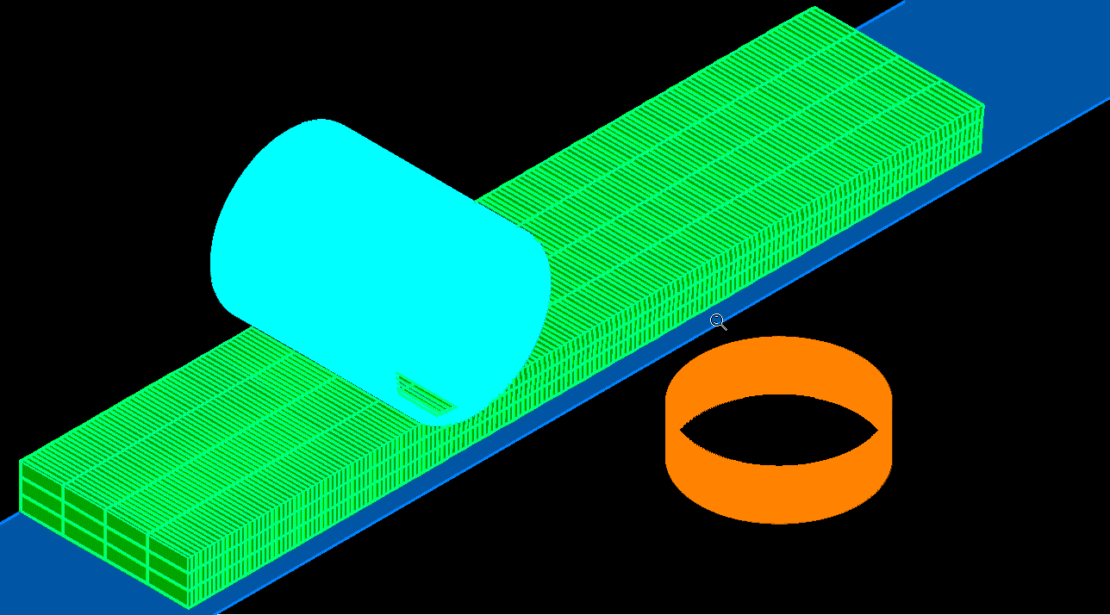
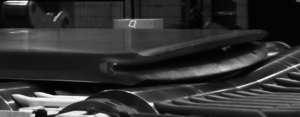
We use FEA models of rolling mills, such as the one in Figure 1, to predict things like alligatoring of ingots (Figure 2). In this case, we only need to model one quarter of the ingot due to symmetry planes.
It’s possible to minimise alligatoring by adjusting the rolling schedule. This is important because less alligatoring means less of the ingot is cropped off. Consequently, waste is minimised.
Figure 3 shows a full 3D simulation of the whole ingot at the end of the ninth pass. The alligator opens up as it moves into the roll bite before closing once it’s in the roll bite.

FEA models and the Innoval Rolling Model
Innoval also has an accurate fast-running analytical rolling model to predict roll loads, torques and other physical quantities. We have used FEA models to develop our rolling model by predicting, for example, forward slip. This is how much faster the slab exits the roll bite compared to the roll surface speed. Two dimensional FEA simulations predict the forward slip as a function of friction, Figure 4.
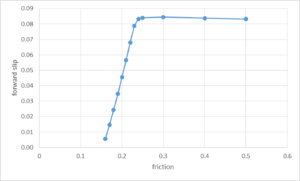
We use the same FEA models to study the velocity of material through the roll bite at three points. These are the roll bite entry, the exit and the neutral point, Figure 5. The neutral point is where the ingot surface speed matches the roll speed. The roll surface speed is 1 m/s in this example. Understanding this type of behaviour helps us to develop more accurate analytical models.
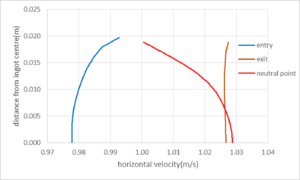
Typically the mill should run in a mode that is optimum for the process as a whole. This means the processes upstream and downstream of the mill need to be considered. This is where we can use some of our many other process modelling tools to find the optimum conditions for the line or product.
FEA models for tension levelling
A levelling process is often carried out after rolling and we have two models that can simulate this. These are the Innoval Tension Leveller Model and an FEA simulation of a roller leveller. Figure 6 shows a screen shot of the Innoval Tension Leveller Model. The geometry of the rolls and strip are in the top window. The bottom window shows the strip through thickness stresses and strains. It’s an extremely fast and user friendly model.
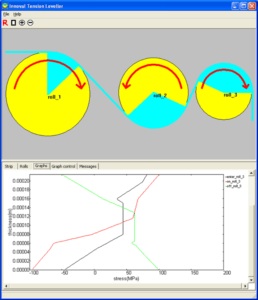
The FEA model of a roller leveller in Figure 7 shows a sheet entering a series of rolls along with the contact forces. It can predict the properties of sheet exiting the leveller which helps the operator set up the machine.
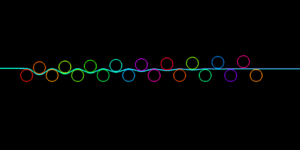
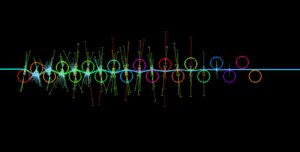
Process cost models
Finally, when there are a number of machines to optimise in a process chain, understanding and calculating the costs can become very complicated. Whilst our Process Cost Models are not FEA models, they are often used in conjunction with them to optimise an entire process. Furthermore, we have experienced specialists who can calculate the costs to assist in making strategic financial decisions.
If you would like to find out more about our modelling capabilities please contact us.
This blog post was originally written by Dr Rade Ognjanovic who has now left the company. Please contact Kyle Smith if you have any questions.